Table of Contents
Manufacturing App Development for the Digital-First World
Author
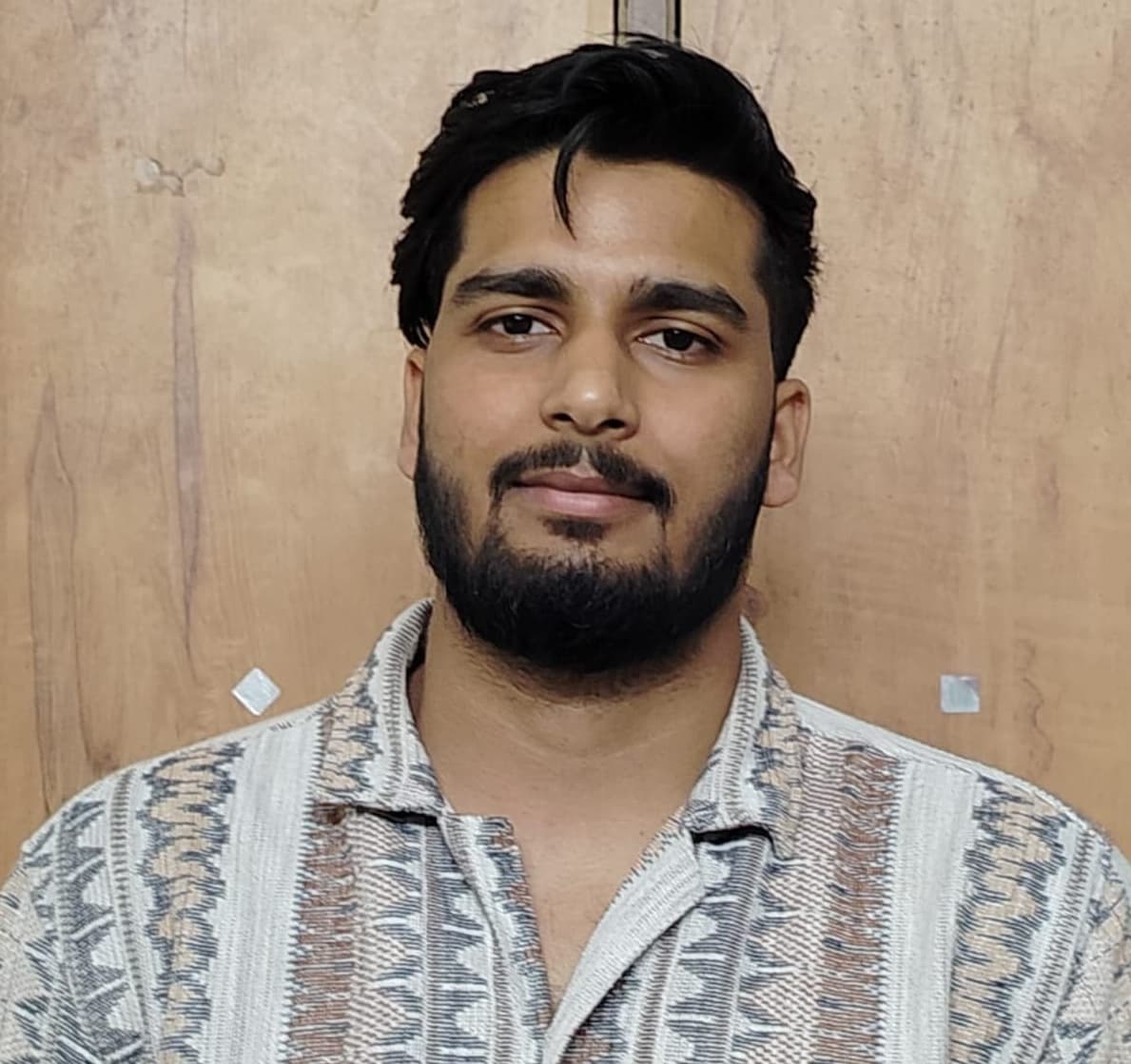
Date
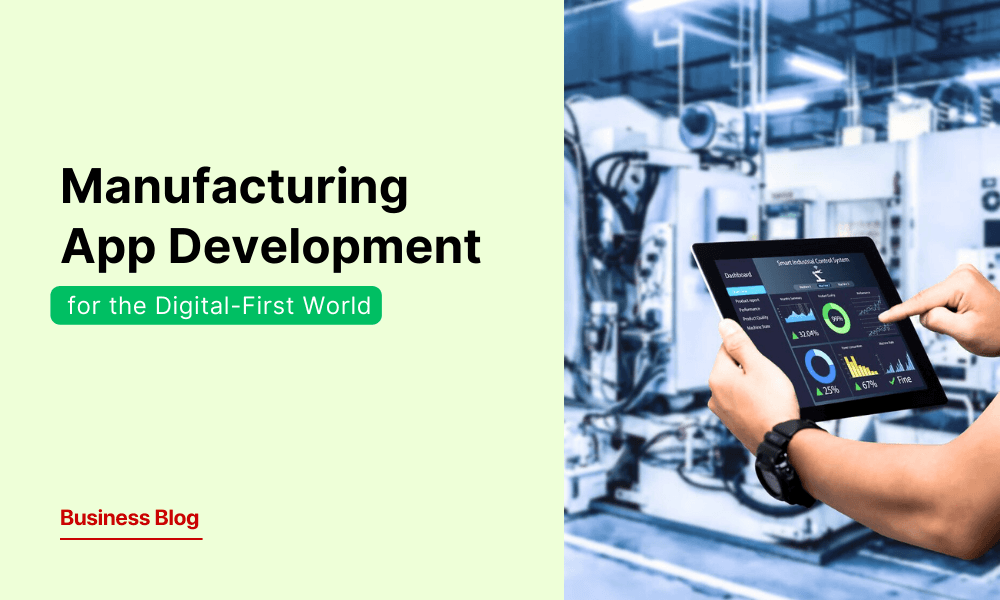
Book a call
In 2023, General Motors (GM) set a benchmark for digital transformation in manufacturing by leveraging generative AI to redesign key car components. This groundbreaking initiative resulted in lighter, more cost-effective parts, reducing material costs by 15% and enhancing vehicle performance, as outlined in GM’s innovation report. This example underscores a pivotal shift in the manufacturing sector: the growing reliance on advanced technologies to overcome industry challenges.
Manufacturing remains a cornerstone of the global economy, contributing nearly 16% to global GDP and employing over 500 million people, as highlighted by the International Labour Organization. However, traditional systems, characterized by inefficiencies like siloed data and reactive processes, are increasingly insufficient in meeting rising consumer demands for efficiency, quality, and sustainability. To stay competitive, manufacturers must adopt digital-first strategies, embracing technologies such as IoT, AI, and cloud computing to streamline operations, enable real-time collaboration, and drive data-informed decisions.
This blog explores how these digital-first approaches and tailored applications are revolutionizing manufacturing, equipping businesses to boost productivity, foster innovation, and secure a competitive advantage in an ever-evolving global landscape.
The Rise of Digital Transformation in Manufacturing
The manufacturing industry is in the process of transitioning from a traditional industry heavily relying on physical assets to a highly digitised modern industry. According to Deloitte, over 72% of consumers now expect personalized products, compelling manufacturers to adopt more flexible and agile production systems. This shift requires integrating technologies that can handle customization at scale while maintaining efficiency. Additionally, McKinsey highlights that optimizing supply chains through advanced tools can reduce logistics costs by 15–20%, a critical factor in navigating increasingly complex global operations. Regulatory compliance further accelerates this transformation, with PwC noting that digital tools enhance tracking and reporting capabilities, mitigating risks and fostering transparency.
However, the path to transformation is not without challenges. Traditional manufacturing systems are often hindered by inefficiencies and limitations that prevent real-time responsiveness. BCG research reveals that conventional factories operate at only 60–70% efficiency, leading to significant resource wastage. High maintenance costs compound these inefficiencies, with the Aberdeen Group estimating that reactive maintenance contributes to $50 billion in unplanned downtime annually. Additionally, Gartner highlights the pervasive issue of siloed data, which obstructs real-time decision-making and slows responses to dynamic market demands. Overcoming these barriers is essential for manufacturers aiming to remain competitive in an increasingly digital-first world.
Core Features of Manufacturing Apps
Real-Time Monitoring and Analytics
Modern manufacturing thrives on real-time data. Apps collect and process data from various sources, enabling manufacturers to make quick, informed decisions.
Example: One of our clients implemented a custom dashboard, leading to a 20% boost in operational efficiency within three months.
Predictive Maintenance and Downtime Reduction
By leveraging machine learning, predictive maintenance anticipates equipment failures before they occur. This approach can reduce unplanned downtime by up to 40% and significantly extend machinery lifespan.
Example: Caterpillar saved over $1.5 million annually using predictive maintenance tools.
Inventory and Supply Chain Management
Efficient supply chains are critical to manufacturing success. Apps offer real-time inventory tracking, demand forecasting, and order optimization. This reduces holding costs by 15-30% and prevents stockouts.
Quality Assurance with AI-Driven Defect Detection
AI-powered quality assurance systems detect defects early in the production process, ensuring high standards and reducing waste.
Example: A GeekyAnts-developed app for a textile manufacturer decreased defect rates by 25%, cutting rework and material costs.
Energy Management and Sustainability
With rising energy costs, manufacturers turn to apps that optimize energy use. These tools monitor consumption patterns and suggest ways to reduce energy waste, aligning operations with sustainability goals.
Worker Safety and Training
Manufacturing apps enhance workplace safety by providing real-time hazard alerts and virtual training modules. These features minimize accidents and improve workforce productivity.
Example: A leading manufacturing firm reported a 15% drop in workplace incidents after integrating safety features in its custom app.
By integrating these features, manufacturing apps transform operational workflows, driving efficiency and innovation in a highly competitive industry.
Emerging Technologies in Manufacturing App Development
1. Integration of IoT, AI, and Big Data
IoT (Internet of Things) devices in manufacturing are used to gather real-time data from machinery and operations. This data is then processed by AI algorithms to predict performance issues or bottlenecks, while Big Data tools analyze trends and patterns to optimize workflows. The combination of these technologies empowers manufacturers to make data-driven decisions, boosting productivity and reducing waste.
Example: General Electric (GE) uses IoT sensors connected to AI and Big Data to predict maintenance needs across its industrial machinery, saving millions in downtime and preventing costly repairs. This approach has helped GE increase its production efficiency while reducing operational costs.
2. Digital Twins and Their Role in Process Simulation
Digital twins are virtual replicas of physical assets or processes, allowing manufacturers to simulate operations and optimize them before real-world implementation. This technology minimizes errors and boosts decision-making accuracy.
Example: GeekyAnts developed a custom digital twin solution for a manufacturing client, simulating their entire production line to identify inefficiencies. The implementation led to a 25% increase in production efficiency, reducing operational costs and enhancing overall workflow management
3. Design and R&D Affected by Generative AI
Generative AI is transforming design and R&D in manufacturing. By using algorithms to generate optimized designs, generative AI enables manufacturers to find the most efficient and cost-effective solutions, reducing product development times and costs. This technology can evaluate millions of design possibilities in a fraction of the time it would take a human designer.
Example: A notable example is how General Motors (GM) uses generative design to develop car parts. GM's AI algorithms analyze a set of constraints and requirements and create lighter, more efficient designs that are both cost-effective and high-performing. The use of generative AI has led to significant savings in material costs and improved vehicle performance.
Benefits of Manufacturing Apps
1. Improved Efficiency and Cost Reduction
Manufacturing apps automate processes and optimize operations, leading to reduced waste and more effective use of resources. These improvements can result in cost reductions of up to 25%, especially by streamlining inventory management and production workflows.
2. Enhanced Decision-Making Through Data Insights
Manufacturing apps provide real-time dashboards that allow managers to access critical insights about machine performance, production status, and inventory levels. This leads to quicker, data-driven decisions that enhance operational effectiveness.
3. Scalability and Flexibility in Operations
Apps provide manufacturers the ability to scale production seamlessly as demand changes. Whether expanding production lines or adapting to market shifts, apps ensure flexibility without requiring significant infrastructure changes. This scalability supports the long-term growth and sustainability of manufacturing businesses.
Case Studies: Successful Manufacturing App Implementations
A leading European railway company sought to improve asset management and reduce downtime in their operations. GeekyAnts developed a comprehensive solution, integrating IoT with a custom web and mobile app. This allowed real-time monitoring of assets, reducing unplanned downtime by 30% and improving overall operational efficiency.
For a deeper dive into how GeekyAnts transformed their processes, check out the full case study: Digital RailwaySolution.
Developing Manufacturing Apps: Best Practices
1. User-Centric Design Principles
Manufacturing apps must be intuitive and easy to use, especially for factory workers who may not have extensive technical experience. A user-friendly interface with clear navigation, visual cues, and a minimal learning curve is essential. Customizing workflows based on user needs ensures smooth onboarding and quick adoption, reducing resistance to new technology.
2. Security and Compliance Considerations
Manufacturing apps must adhere to stringent security protocols to protect sensitive data. This includes encryption, user authentication, and access control. Compliance with industry standards like ISO 27001 and GDPR ensures that data is handled responsibly and meets regulatory requirements, minimizing legal risks and safeguarding intellectual property.
3. Integration with Legacy Systems
To avoid disrupting existing operations, manufacturing apps should seamlessly integrate with legacy systems. This prevents costly system overhauls and allows real-time data exchange between new and old systems, ensuring smoother transitions and enhanced efficiency. By integrating with established systems, businesses can leverage their current infrastructure without significant downtime or loss in productivity.
A Corner of GeekyAnts
At GeekyAnts, we specialize in developing custom apps that enhance manufacturing and technology operations. Our solutions optimize efficiency, improve user experiences, and drive digital transformation.
For example:
- E-Sports Gaming Platform for MPL: We built a scalable gaming platform that supports millions of users, enhancing engagement and ensuring seamless functionality across platforms.
- P2P App for the @ Company: A privacy-focused app designed to transform online experiences, offering enhanced privacy features and greater accessibility for users.
For more details, check out our full case studies.
Conclusion
The future of manufacturing is digital. Embracing custom apps is no longer optional—it is the key to unlocking unparalleled efficiency, quality, and sustainability. From reducing downtime to streamlining inventory management, these solutions are transforming the industry and setting new benchmarks for success.
At GeekyAnts, we don’t just deliver apps; we deliver results. Whether it’s helping a railway company cut downtime by 30% with IoT-driven monitoring or enabling a textile manufacturer to reduce defect rates by 25% with AI-powered solutions, our expertise drives real-world impact. We’re here to help manufacturers lead in this digital-first era, turning challenges into opportunities and innovation into measurable success.
Dive deep into our research and insights. In our articles and blogs, we explore topics on design, how it relates to development, and impact of various trends to businesses.